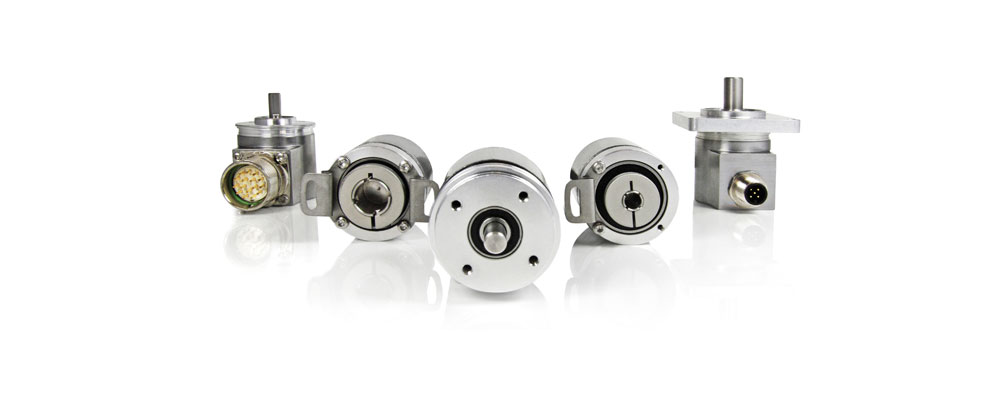
Understanding Rotary Encoders terminologies is crucial when working with or selecting encoders for various applications. In this blog post, we’ll explore some of the essential terminologies related to rotary encoders, helping you gain a better understanding of their features and specifications.
A
Absolute Rotary Encoders
Absolute rotary encoders are sensors that provide position information for rotating shafts or motors. Unlike incremental encoders, absolute encoders give a unique digital code for each position of the shaft, providing an absolute position measurement without the need for a reference point.
This allows the system to instantly know the precise position of the shaft at any given time, making them ideal for applications requiring high accuracy and precision. Absolute rotary encoders can be further classified into single-turn and multi-turn encoders, depending on their ability to measure the number of rotations. These sensors are widely used in industrial applications such as robotics, CNC machines, and medical devices.
Ambient Humidity
Ambient humidity refers to the level of moisture present in the air surrounding an object or environment. It is typically measured in percentage and can have a significant impact on the performance and lifespan of certain equipment or materials.
For example, high humidity levels can cause corrosion, mold growth, and electrical issues in electronics and machinery, while low humidity levels can lead to static electricity and damage to sensitive components. Ambient humidity is a critical factor to consider in various industries, including manufacturing, agriculture, and healthcare.
Ambient Temperature
Ambient temperature refers to the temperature of the surrounding environment or the area in which a system or device is located. It is an important factor to consider in various industries, such as manufacturing, where temperature can affect the quality and performance of products and equipment.
In the context of electronic devices, such as sensors and controllers, ambient temperature can impact their accuracy, sensitivity, and reliability. Therefore, it is essential to monitor and control the ambient temperature to ensure the optimal functioning of industrial equipment and systems. The standard unit for measuring temperature is Celsius (°C) or Fahrenheit (°F).
Axial Cable Type
Axial cable type refers to a type of cable where the wires or conductors run parallel to the cable’s axis or centerline. This type of cable is commonly used in rotary encoder applications, where it is important to maintain a consistent signal quality even during rotation.
The axial cable type allows for stable and reliable signal transmission, as the wires are shielded from external interference and do not experience any twisting or stretching during rotation. Overall, the use of axial cable type in rotary encoder applications helps to ensure accurate and consistent data transmission.
C
Cable Type
In the context of rotary encoders, cable type refers to the type of cable used to connect the encoder to the control unit. The cable plays an important role in ensuring the transmission of accurate and reliable signals between the encoder and control unit.
There are various types of cables used for this purpose, including shielded and unshielded cables, twisted pair cables, and multi-conductor cables. The choice of cable type depends on the specific requirements of the application, such as the length of the cable, the level of electromagnetic interference in the environment, and the frequency of the signal. A properly selected cable type helps ensure the optimal performance and longevity of the rotary encoder system.
Connector Type
Connector type in rotary encoders refers to the type of connector used to connect the encoder to the controller or other equipment. There are various connector types available, such as circular connectors, rectangular connectors, and DIN connectors.
The choice of connector type depends on various factors such as the type of equipment being used, the environment in which the encoder will be operating, and the number of signals that need to be transmitted. Some rotary encoders also come with the option of customized connector types to meet specific application requirements. It is important to select the appropriate connector type to ensure the reliable and accurate transmission of signals.
H
Hollow Type
In rotary encoders, the term “hollow type” refers to encoders that have a hollow shaft through their center, allowing for the shaft of the machine being monitored to pass through the encoder’s center. Hollow-type encoders are commonly used in applications such as robotics, machine tooling, and printing presses, where space is at a premium and it is essential to maintain the axial position of the machine shaft.
By using a hollow-type encoder, the encoder can be mounted directly onto the machine shaft, minimizing any inaccuracies that may occur due to mechanical misalignment. The use of a hollow-type encoder also allows for simpler installation, as there is no need for additional coupling mechanisms.
I
Incremental Rotary Encoders
Incremental rotary encoders are sensors that provide position and/or speed feedback by generating a series of digital pulses as the encoder shaft rotates. Each pulse represents a small angular displacement, and the number of pulses per revolution determines the resolution of the encoder. Incremental encoders can provide high accuracy and precision in applications such as motion control, robotics, and industrial automation. However, they do not provide absolute position information and require a reference point to be established at a startup. As the shaft rotates, the incremental encoder tracks the movement and provides incremental position feedback, but the absolute position of the shaft cannot be determined unless the reference point is known.
Ingress Protection rating
Ingress Protection (IP) rating is a measure of the level of protection provided by an enclosure against the intrusion of solid objects, dust, and moisture. The IP rating consists of two digits, the first indicating the degree of protection against solid objects and the second indicating the degree of protection against moisture.
The higher the number, the better the protection. For example, an IP67 rating means that the enclosure is completely protected against dust and can be submerged in water up to 1 meter for 30 minutes. IP ratings are important when selecting a rotary encoder for use in harsh environments, such as in industrial or outdoor applications.
L
Line Drive Output
Line Drive Output is a type of output signal that is commonly used in rotary encoders. It is a type of digital output signal that is used to send information about the position or movement of the encoder to other electronic devices, such as programmable logic controllers (PLCs) or other industrial automation equipment.
In a line drive output, the encoder sends out a constant voltage signal, which is either high or low depending on the position of the encoder. This signal is then interpreted by the receiving device to determine the position or movement of the encoder. Line drive outputs are often used in harsh industrial environments, as they are resistant to electrical interference and other types of noise.
M
Magnetic Rotary Encoders
Magnetic rotary encoders are a type of rotary encoder that uses magnetic fields to detect the rotational position of a shaft. They consist of a rotating shaft with a magnetic field and a sensing element that detects changes in the magnetic field. The sensing element can be a Hall-effect sensor or a magneto-resistive sensor.
Magnetic rotary encoders are known for their high accuracy, high resolution, and ability to operate in harsh environments. They are often used in applications such as robotics, medical equipment, and industrial automation. Magnetic rotary encoders can be either absolute or incremental, depending on the type of sensing element used.
Moment of Inertia
Moment of Inertia refers to a property of an object that measures its resistance to rotational motion. In the context of rotary encoders, a moment of inertia is an important consideration as it affects the encoder’s ability to accurately detect changes in rotational position.
The moment of inertia of an encoder is affected by various factors, including the size and shape of the encoder, as well as the distribution of mass within the encoder. In general, encoders with larger moments of inertia are better suited for applications where the load being measured is heavy or where there are significant changes in rotational speed.
When selecting a rotary encoder, it is important to consider the moment of inertia of the encoder in relation to the application’s requirements. A mismatch between the encoder’s moment of inertia and the load being measured can result in inaccuracies and errors in the measured values.
Mounting Options
Mounting options refer to the different ways in which rotary encoders can be installed in a system. Depending on the application requirements and available space, different mounting options can be chosen.
Some common mounting options for rotary encoders include:
Shaft mount: The encoder is mounted directly on the shaft of the motor or other rotating equipment.
Flange mount: The encoder is mounted on a flange attached to the motor or other rotating equipment.
Base mount: The encoder is mounted on a base attached to the motor or other rotating equipment.
Servo mount: The encoder is mounted on the rear of the motor, and its position is synchronized with the motor’s position.
Hollow shaft mount: The encoder is mounted around the shaft of the motor or other rotating equipment.
The choice of mounting option can impact the accuracy and reliability of the encoder’s output. It is important to carefully consider the mounting option that best suits the application’s needs.
Multi-turn Encoders
Multi-turn encoders are rotary encoders that are capable of measuring more than one full revolution of the encoder shaft. These types of encoders have an additional gear or worm mechanism that allows them to count the number of turns beyond one revolution.
Multi-turn encoders can be absolute or incremental, and they are commonly used in applications where precise position and motion control are required over long distances or multiple revolutions. Some common applications of multi-turn encoders include robotic arms, machine tools, material handling equipment, and industrial automation systems.
N
NPN Output
NPN output refers to a type of output signal in rotary encoders and other types of sensors that are used in industrial automation. NPN stands for Negative-Positive-Negative, which refers to the type of electrical configuration used in the output circuitry of the sensor.
In NPN output, the signal is pulled to a negative voltage when activated and is at a high impedance or “floating” state when not active. This type of output signal is commonly used in applications where the signal is sent to a PLC or other control system that requires an NPN input signal.
O
Optical Rotary Encoders
Optical rotary encoders are types of rotary encoders that use a light source, such as a LED, to detect the movement of a rotating object. The encoder contains a rotating disk or a strip with alternating transparent and opaque sections, which interrupts the light beam from the light source as it rotates.
A photo-detector or photodiode is used to detect the changes in the light intensity caused by the rotating disk or strip and generates an electrical signal that can be used to determine the position, speed, or direction of the rotating object. Optical rotary encoders are known for their high accuracy, resolution, and reliability, and are commonly used in industrial automation, robotics, CNC machines, and other applications that require precise motion control.
Output Phase
The output phase refers to the relationship between two or more output signals of a rotary encoder. In the case of incremental encoders, output signals are typically referred to as A, B, and Z. The A and B channels are the primary signals used to determine the position and direction of rotation. The Z channel is a once-per-revolution pulse used as a reference marker.
The output phase can have different configurations, including single-ended, differential, and open collector. Single-ended output phase refers to the use of one signal wire for each output signal. The differential output phase, on the other hand, uses two wires for each signal, with one wire carrying the signal and the other wire carrying the inverted signal. Open collector output phase is a type of single-ended output phase where the output signal is connected to an open collector transistor, which can be connected to an external power supply to provide a high-level signal. The choice of output phase configuration depends on the specific requirements of the application.
P
PNP Output
PNP Output refers to a type of output signal provided by a rotary encoder. In a PNP output, the encoder provides a positive voltage signal in relation to the ground reference level. This type of output is commonly used in industrial automation applications and is often preferred for its simplicity and compatibility with a wide range of systems.
The PNP output signal is also known as a sourcing output, as the encoder sources current to the load. PNP outputs can be easily interfaced with a variety of digital devices and can be used in conjunction with other types of sensors for increased functionality and flexibility in control systems.
Power Supply
Power supply in rotary encoders refers to the electrical input required to operate the encoder. It is important to ensure that the encoder is receiving the correct voltage and frequency of the power supply, as specified in the manufacturer’s instructions. Most rotary encoders operate on a DC power supply, with a voltage range typically between 5V to 30V.
Some encoders may also operate on AC power. It is important to note that a stable and reliable power supply is critical for the accurate and reliable operation of the encoder, and any fluctuations or disruptions in the power supply can result in errors or malfunctions.
Pulse per Revolutions
Pulse per revolution (PPR) is a term used to describe the number of electrical pulses generated by a rotary encoder for each full rotation of the shaft. It is a measure of the encoder’s resolution and determines the level of precision and accuracy that can be achieved in position sensing and control applications.
The PPR value depends on the design and specifications of the encoder and can range from a few pulses per revolution to thousands or even millions of pulses per revolution for high-resolution encoders. A higher PPR value generally results in higher accuracy and finer resolution, but also increases the cost and complexity of the encoder and associated control systems.
Push Pull Output
Push Pull Output refers to a type of output signal in rotary encoders, which is commonly used in industrial automation applications. In this output configuration, the encoder sends two signals (high and low) for each pulse or increment, one for the positive side and one for the negative side.
This results in a more reliable and robust signal that can be transmitted over longer distances without degradation. Push-pull output is compatible with a wide range of electronic equipment and is often used in applications that require a high-speed operation, precision control, and immunity to noise and interference. It is a popular choice for motion control systems, robotics, and CNC machines.
R
Radial Connector Type
The radial connector type is a type of connector used in rotary encoders that allows the cable to be connected from the side of the encoder. This is in contrast to the axial connector type where the cable is connected from the end of the encoder. Radial connectors are commonly used in applications where space is limited and where it is necessary to have a low profile.
They also provide a more secure connection as the cable is held in place by the connector. However, radial connectors may not be suitable for all applications, as they may require additional clearance around the encoder for cable routing.
Response Time
Response time refers to the time required by a sensor to detect and report a change in the parameter it is measuring. In rotary encoders, response time refers to the time taken by the sensor to detect a change in the rotational movement of the shaft and report it as an output signal. The response time of an encoder is an important parameter that determines the accuracy and reliability of the measurements.
A shorter response time indicates faster and more precise measurements, while a longer response time may result in delayed or inaccurate measurements. The response time of rotary encoders can vary depending on the type, design, and application of the encoder.
S
Shaft Dia
Shaft Dia, short for Shaft Diameter, refers to the width or size of the shaft that the encoder is mounted on. The shaft diameter of an encoder is important because it determines whether the encoder can be mounted onto the particular motor or machine. Inaccurate or incompatible shaft diameters can cause misalignment and lead to errors in encoder readings, which can negatively impact the performance of the machine or system.
Therefore, it is important to select an encoder with the appropriate shaft diameter to ensure a proper fit and accurate readings. Shaft diameters are typically measured in millimeters or inches, depending on the unit of measurement used in a particular country or region.
Shaft Loading
Shaft loading refers to the maximum amount of force that can be applied to the shaft of a rotary encoder without causing damage. It is an important consideration when selecting an encoder for an application because excessive loading can cause premature failure of the encoder or reduce its accuracy.
The amount of shaft loading that an encoder can withstand depends on various factors such as the material and diameter of the shaft, the bearings used in the encoder, and the type of load applied. It is important to select an encoder with a shaft loading rating that exceeds the maximum load that will be applied in the application to ensure reliable and accurate operation.
Shaft Type
Shaft type refers to the shape and design of the output shaft of a rotary encoder. The output shaft of an encoder is the part of the encoder that rotates and transmits the measurement information. Different types of shafts are used in different applications, depending on factors such as torque requirements, mounting requirements, and the environment in which the encoder will be used.
Some common types of shafts used in rotary encoders include solid shafts, hollow shafts, and blind hollow shafts. Solid shafts are generally used in applications with low torque requirements, while hollow shafts are used for applications where the encoder needs to be mounted directly onto the driven shaft. Blind hollow shafts are used when the encoder must be mounted onto a separate shaft adapter.
Shock
In the context of rotary encoders, shock refers to the resistance of the encoder to sudden mechanical impacts or vibrations. Rotary encoders are commonly used in industrial applications where machinery and equipment may be subjected to sudden shocks, such as during heavy-duty manufacturing processes or in automotive applications. Encoders with high shock resistance are important to ensure accurate and reliable operation of the equipment.
The shock resistance of an encoder is typically measured in units of g (acceleration due to gravity) and is specified in the encoder’s datasheet. Manufacturers may also provide information on the encoder’s shock resistance in terms of its ability to withstand specific impact forces or vibrations.
Single-turn Encoder
A single-turn encoder is a type of rotary encoder that can provide information on the position of a rotating shaft within a single revolution. It has a resolution that is limited to a single turn and can only detect the absolute position of the shaft within that turn. Single-turn encoders are typically used in applications where a single turn of the shaft is sufficient to measure the position or speed of a machine or system.
They are commonly used in robotics, CNC machines, printing presses, and other industrial applications. Single-turn encoders are available in various designs, including optical and magnetic encoders, and they can use different output signals, such as digital, analog, or serial.
SSI Interface
SSI stands for “Synchronous Serial Interface,” which is a widely used serial communication protocol for industrial automation applications. SSI interface is a synchronous, point-to-point interface that allows data exchange between a master device, such as a programmable logic controller (PLC), and a slave device, such as an absolute encoder.
SSI interface is typically used for high-precision and high-resolution applications that require accurate measurement and control, such as motion control systems, robotics, and machine tools. SSI interface provides a high level of noise immunity and supports long-distance communication, making it ideal for industrial environments. It is important to note that the SSI interface is a digital interface, which means it provides discrete data output rather than continuous signals.
Starting Torque
Starting torque refers to the amount of torque required to start the rotation of a system. In the case of rotary encoders, starting torque is the amount of torque required to initiate the rotation of the encoder shaft. It is an important specification to consider as it can affect the accuracy and reliability of the encoder’s readings.
A high starting torque requirement can indicate that the encoder may be more prone to errors or mechanical issues, while a low starting torque requirement may indicate a more efficient and reliable system. The starting torque is often specified in the encoder’s datasheet and can vary depending on the type and model of the encoder.
V
Vibration
Vibration refers to the back-and-forth motion of an object or surface, usually caused by an external force. In the context of rotary encoders, vibration can affect the accuracy and reliability of the encoder’s measurements. Excessive vibration can cause the encoder to produce erroneous readings, which can lead to issues in industrial applications that rely on precise measurements.
To mitigate the effects of vibration on rotary encoders, manufacturers often design encoders with features such as shock resistance, high-frequency response, and rugged construction. In addition, it is important to properly mount and install the encoder to minimize any external vibrations that may affect its performance.
W
Wheel Type Encoder
A wheel-type encoder is a type of rotary encoder that utilizes a wheel with evenly spaced teeth or slots to generate electrical signals as the wheel rotates. The wheel is typically made of a magnetic or conductive material, and the teeth or slots are detected by a sensor, such as a photoelectric sensor or a Hall-effect sensor, to generate a series of pulses. These pulses can be used to determine the position, speed, and direction of rotation of the wheel.
Wheel-type encoders are commonly used in industrial applications where precise motion control is required, such as in robotics, packaging machinery, and conveyor systems. They are known for their high accuracy, reliability, and resistance to wear and tear, making them a popular choice for demanding environments. Some common types of wheel-type encoders include optical encoders, magnetic encoders, and capacitive encoders.
Conclusion
These terminologies are commonly used in rotary encoders and are important to understand their functionality and specifications. From types of encoders such as absolute, incremental, magnetic, and optical, to parameters such as shaft loading, mounting options, and response time, each aspect plays a crucial role in the performance of the encoder.
In addition, factors such as ingress protection rating, shock, and vibration resistance must be considered for the encoder to function in harsh environments. Understanding these terminologies will aid in the selection and operation of rotary encoders for various industrial applications.